The complete melting of the filler ends in a dense layer with optimal adhesion to the substrate. The most typical software is for the damage safety, e.g. of tools, but also corrosion safety or high temperature resistance may be specifically improved. Common exhausting alloys based on cobalt, nickel and iron are used with and with out the addition of exhausting materials. But also particularly adapted materials could be applied.
The constants a and b are fundamental properties of the fabric and can be decided from commonplace laboratory experiments on recent fuel. In explosive welding, a compression pressure created by detonation of explosives is used to affix overlapping metallic sheets. The becoming a member of parts are arranged in the direction of each other at an angle of 1–15°, depending on the fabric and methodology, and are ready with a layer of explosive on the highest. After ignition the becoming a member of areas are moved towards one another at excessive velocity.
In addition to metallurgical elements, water chemistry has a strong affect on the corrosion course of in zirconium alloys. The management of water chemistry as required in different reactor systems embrace appropriate additions of lithium hydroxide, boric acid, hydrogen/deuterium, oxygen, iron, and zinc. In PWRs, boric acid is added to the coolant water for reactivity management. The pH of the coolant is adjusted by addition of lithium hydroxide which renders the coolant slightly alkaline, to be able to reduce the corrosion rates of structural supplies (stainless steels and Inconels) in the major warmth transport circuit and thereby inhibit deposition of corrosion merchandise on the fuel cladding. Radiolysis of water produces oxidizing species which reinforces oxidation rate of zirconium alloys in the radiation environment .
The melt layer is sort of thin; for instance, when cladding an aluminum alloy it's about 0.5–4μm (Kreye 1985, 1997 ). The dilution of the molten zones ends in plane or corrugated interfaces. During mechanical decladding, the gas assemblies are chopped and the gasoline core is leached with nitric acid, abandoning the undissolved cladding material for disposal as a solid waste.
Its business identify is Zircaloy, or Zry for short. Zry comes in two varieties, Zry-2 and Zry-4. These two differ by minor adjustments in the concentrations of the transition metals (Zry-four has no nickel). PWRs use Zry-four while BWRs employ Zry-2 as cladding and either Zry-2 or Zry-4 for the duct or channel holding the gas-component bundle.
The compromise between these competing calls for has produced wall thicknesses of ∼zero.9mm in BWRs and ∼zero.7mm in PWRs. Laser cladding usually entails covering a relatively cheap substrate material with a dearer alloy that will improve the resistance of the half to wear or corrosion.
Zircaloys additionally undergo from unhealthy creep charges. In contrast to floor-layer welding, explosive welding causes no change in microstructure, and corrosion resistance of the layers just isn't affected (Pocalco 1987 ).
In PWRs the closure of the hole between the pellet and the clad takes about one full energy year while the hole is maintained for an extended period in BWRs. Due to the collapsible clad design of PHWRs, contact between the pellet and the clad is established right from the beginning of the lifetime of the gas component. Laser coating or laser cladding can be used to domestically functionalize metallic elements. In this course of, an edge layer of sometimes 0.1 to 2 mm is utilized to the component. The coating material employed is either powder or wire, or utilized prematurely as a tape.
As a treatment, speedy cooling of the Zry ingot during fabrication (known as beta quenching) produces a a lot finer intermetallic precipitate inhabitants. This distribution of the transition metals maintains the strength of the Zry however improves its corrosion resistance, presumably by quick-circuiting cost-transport paths between the dimensions floor and the steel–oxide interface. In order to remove waterside corrosion of cladding as a life-limiting process, modified Zircaloys have been developed. Under PWR water situations, lowering the tin content of Zry to 1% and including a comparable concentration of niobium produces an alloy with a corrosion price several times lower than that of the usual Zry. Modified low-tin alloys can be utilized both as an entire alternative for the Zry tube wall or as a thin outer skin on standard Zry substrate tubing.
Joining occurs continuously by local plastic deformation of the contact space (Ruge 1993 ) (see Fig. 1 ). Figure 6 . Schematic diagram displaying the mechanism of the oxidation course of and the oxide film construction on zircaloy. Figure 5 .
This technique is adopted for zircaloy-clad fuels from energy reactors and chrome steel-clad quick reactor fuels. Like the cladding , under the impact of neutron flux the hexagonal wrapper tube undergoes change. Geometrical modifications, induced by swelling and irradiation creep (underneath the effect of dynamic sodium stress), concern length, throughout-flat dimension, and, for subassemblies placed in the periphery of the core, bowing (differential swelling induced by differential flux and temperature between reverse faces of the wrapper tube).
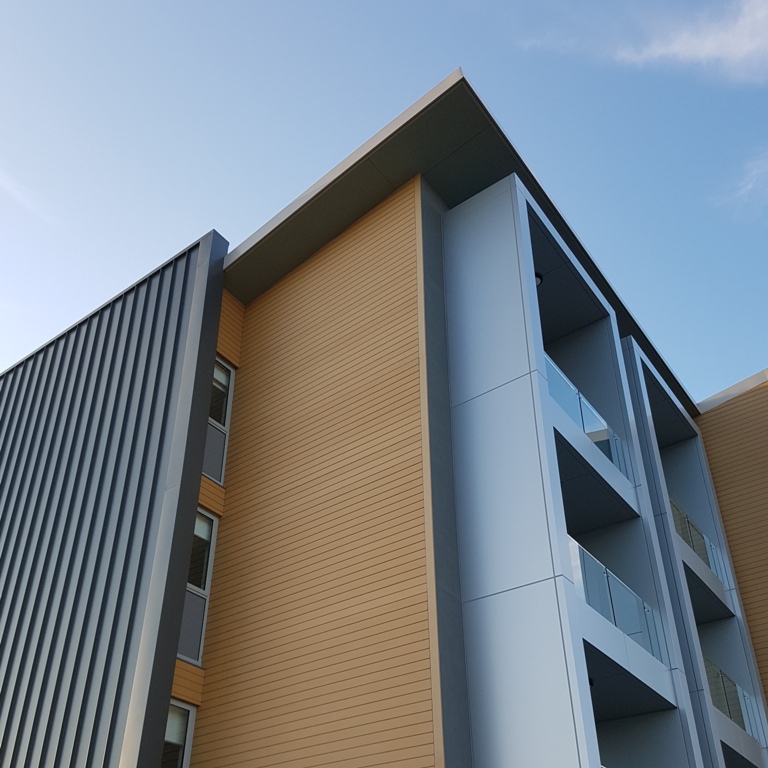
Metallverkleidung f
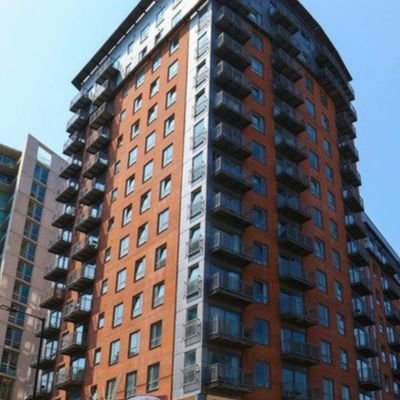
Its business identify is Zircaloy, or Zry for short. Zry comes in two varieties, Zry-2 and Zry-four. These two differ by minor modifications within the concentrations of the transition metals (Zry-4 has no nickel). PWRs use Zry-four while BWRs employ Zry-2 as cladding and either Zry-2 or Zry-4 for the duct or channel holding the gasoline-factor bundle.
The thickness of the cladding might differ between zero.1 and 30 mm and the detonation velocity is between 1200 and 7000 ms −1 . The high plate hits the bottom plate with a speed of one hundred–1000 ms −1 , and pressures are in the vary of 10 to a hundred kbar. Under certain situations a superheated layer of material forms within the contact space. The joint is then brought on by a deformation-induced melting bathtub.
Enhance the curb enchantment of your house with B&Q cladding. All of our timber is responsibly sourced forest friendly timber.
This methodology is adopted for zircaloy-clad fuels from energy reactors and stainless-steel-clad fast reactor fuels. Like the cladding , underneath the impact of neutron flux the hexagonal wrapper tube undergoes change. Geometrical changes, induced by swelling and irradiation creep (under the effect of dynamic sodium pressure), concern size, throughout-flat dimension, and, for subassemblies placed within the periphery of the core, bowing (differential swelling induced by differential flux and temperature between reverse faces of the wrapper tube).
tube. Energy, from fission, is generated approximately uniformly all through the gas pellets. Heat is extracted at the rod floor by the coolant flow. The temperature at the hottest point, at the pellet centerline, is typically in the vary 800–1000 °C, relying on the power stage. The metallic cladding is an effective conductor, so the temperature rise across the wall is just a few tens of degrees.
The course of is usually used to create a protective coating for increased performance, in addition to restore damaged or worn surfaces. Laser cladding allows prolonged life of apparatus and equipment in which elements are exposed to corrosion, put on or impression. For instance, the construction tools trade applies this technology to their merchandise to extend wear resistance and keep gear in service longer. A excessive-power laser is used as the warmth source in laser cladding. During the process, a surface layer is created by the use of melting and the simultaneous application of just about any given material.
The helium filling fuel is also a fairly good conductor, but only as long as it remains uncontaminated by fission products. The poorly conducting ceramic gas pellets are accountable for almost all of the temperature rise. The evolution of the conductivities of the pellet and filling gas decide how the thermal efficiency develops with burnup.
Brochure “Laser Technology More Helpcheck over herehis comment is here for Repair and Functionalization“
As the oxide layer grows, the compressive stress on the outer layer of oxide isn't sustained and consequently the tetragonal phase turns into unstable and transforms into the monoclinic phase. Such a change causes the formation of a nice interconnected porosity in the oxide film which allows the oxidizing water to come in contact with the metallic floor. With the development of an equilibrium pore and crack construction within the oxide layer, the oxidation fee effectively becomes linear, a attribute function of the post-transition oxidation conduct.
The transition metals iron and chromium appear in the microstructure as precipitates of the intermetallic compounds Zr 2 (Ni,Fe) and Zr(Cr,Fe) 2 . These minor alloying components improve corrosion resistance to an extent dependent on the dimensions of the precipitates. Laser cladding has been utilized to hardening of steam generator turbine blades and reached pilot manufacturing status [4 ]. The blades had a machined pocket, into which powdered cobalt-based mostly metallic (Stellite 6) was fed ahead of the laser beam.
The thickness of the cladding could differ between 0.1 and 30 mm and the detonation velocity is between 1200 and 7000 ms −1 . The high plate hits the underside plate with a pace of one hundred–one thousand ms −1 , and pressures are in the vary of 10 to 100 kbar. Under sure circumstances a superheated layer of fabric varieties in the contact area. The joint is then caused by a deformation-induced melting tub.
The effect of thermal conductivity degradation on the efficiency of the fuel is illustrated in Fig. 1 . This exhibits the outcomes of calculations during which the power in a rod is artificially held at a constant stage.
tube. Energy, from fission, is generated roughly uniformly all through the fuel pellets. Heat is extracted on the rod floor by the coolant circulate. The temperature at the hottest level, on the pellet centerline, is typically within the vary 800–one thousand °C, depending on the facility stage. The metallic cladding is an efficient conductor, so the temperature rise across the wall is only some tens of levels.

Cladding (building)

The filler material can both be equipped in powder kind e.g. as metal powder, or with a welding wire. When laser cladding is carried out utilizing powder, the laser normally heats the workpiece with a defocussed laser beam and melts it locally. At the same time, an inert gasoline mixed with a nice metal powder is introduced. The steel powder melts on the heated space and is fused to the floor of the workpiece.
Enhance the curb appeal of your home with B&Q cladding. All of our timber is responsibly sourced forest pleasant timber.
The thickness of the cladding could differ between zero.1 and 30 mm and the detonation velocity is between 1200 and 7000 ms −1 . The top plate hits the underside plate with a speed of one hundred–1000 ms −1 , and pressures are in the vary of 10 to a hundred kbar. Under certain conditions a superheated layer of material forms within the contact area. The joint is then brought on by a deformation-induced melting bath.
Its business name is Zircaloy, or Zry for brief. Zry comes in two varieties, Zry-2 and Zry-4. These two differ by minor changes within the concentrations of the transition metals (Zry-4 has no nickel). PWRs use Zry-four whereas BWRs make use of Zry-2 as cladding and both Zry-2 or Zry-4 for the duct or channel holding the fuel-component bundle.
In addition to metallurgical factors, water chemistry has a strong affect on the corrosion course of in zirconium alloys. The control of water chemistry as required in numerous reactor techniques embrace appropriate additions of lithium hydroxide, boric acid, hydrogen/deuterium, oxygen, iron, and zinc. In PWRs, boric acid is added to the coolant water for reactivity management. The pH of the coolant is adjusted by addition of lithium hydroxide which renders the coolant barely alkaline, to be able to scale back the corrosion charges of structural supplies (stainless steels and Inconels) in the major heat transport circuit and thereby inhibit deposition of corrosion merchandise on the fuel cladding. Radiolysis of water produces oxidizing species which boosts oxidation price of zirconium alloys within the radiation setting .
In one, a second inside-surface liner of ordinary Zry is extruded on the sponge zirconium liner so as to restore corrosion resistance. In other modifications, the sponge zirconium is alloyed with iron or tin to improve oxidation resistance without affecting the softness that gives immunity from PCI. Standard Zry is sufficiently hard to be prone to stress-corrosion cracking (SCC) when the pellet–cladding gap closes and the swelling gasoline generates substantial tensile hoop stresses in the cladding. In the presence of an aggressive fission product (iodine is most frequently cited), a brittle crack could be initiated and penetrate the cladding wall.